How Are Lighters Manufactured Using Production Machines?
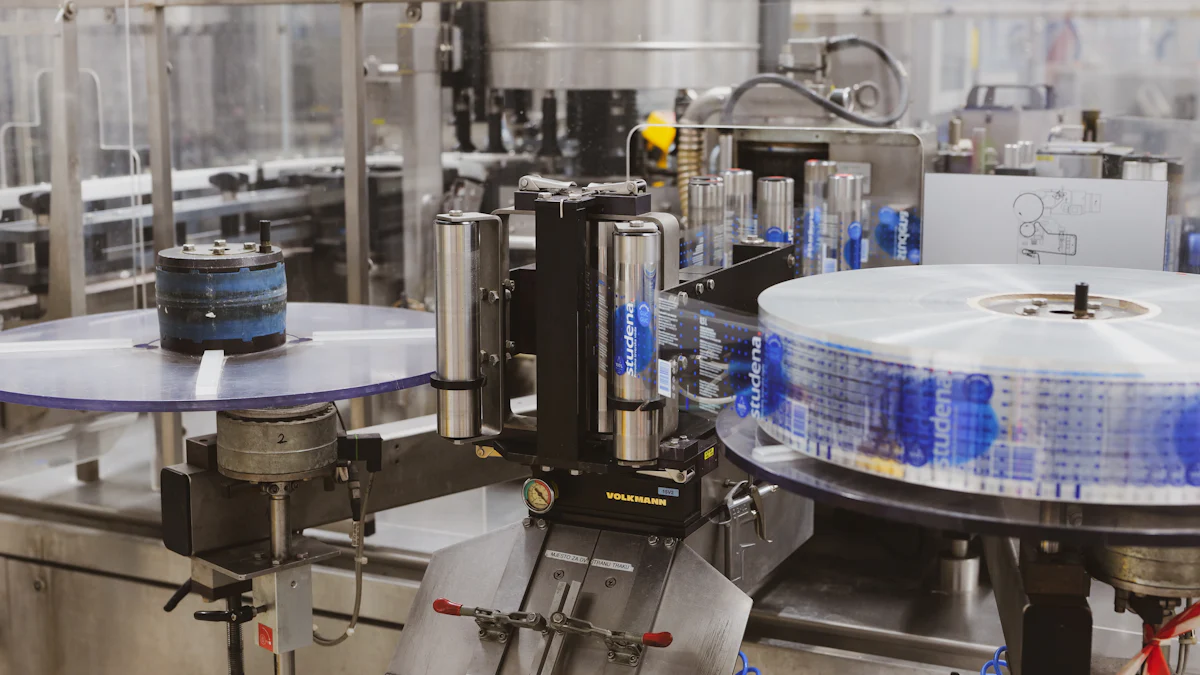
I find the process of manufacturing lighters fascinating. It involves a series of automated steps that use specific materials and techniques. The lighter production machine plays a crucial role in this process. It ensures efficiency and consistency, which significantly reduces labor costs. For instance, automation has increased per capita efficiency by 30 times, lowering the labor cost per lighter from 0.1 yuan to less than 0.02 yuan. These machines also enhance safety standards, with modern production lines conducting over 50 automatic checks to ensure each lighter meets stringent safety requirements. This meticulous approach not only improves throughput but also minimizes environmental impacts.
Key Takeaways
- Lighter production machines significantly enhance efficiency, reducing labor costs and increasing output by automating key processes.
- Choosing the right materials, such as metals for durability and plastics for lightweight design, is crucial for ensuring the functionality and safety of lighters.
- Safety features, including child-resistant mechanisms, are essential in lighter design to prevent accidents and protect consumers.
- The manufacturing process involves meticulous steps, from raw material inspection to automated assembly, ensuring high-quality products.
- Quality control is vital, with thorough inspections and testing to guarantee that each lighter meets safety and performance standards.
- Sustainable practices, such as recycling materials and minimizing waste, are increasingly important in lighter manufacturing to reduce environmental impact.
- Emerging trends like smart lighters and eco-friendly materials are set to revolutionize the industry, promoting safer and more sustainable production methods.
Raw Materials and Design Considerations
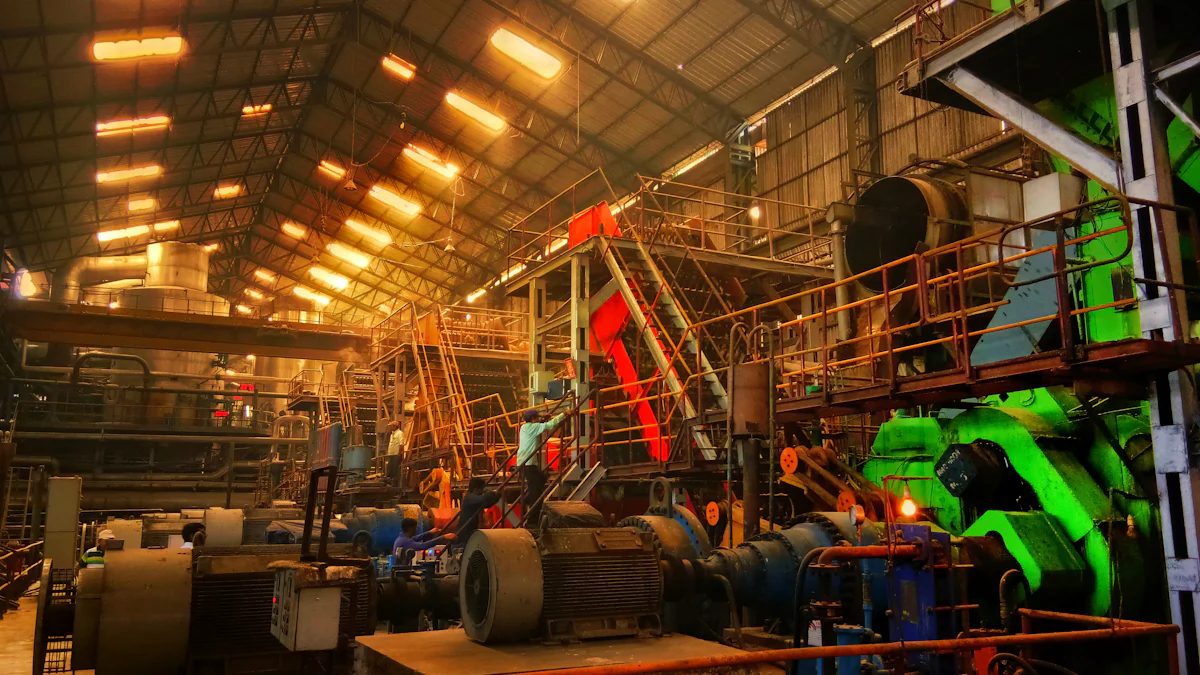
Materials Used in Lighter Manufacturing
In the world of lighter manufacturing, selecting the right materials is crucial. I have observed that each component plays a specific role in ensuring the lighter’s functionality and safety.
Metal Components
Metal components form the backbone of many lighters. They provide durability and structural integrity. For instance, the BIC lighter uses metals like steel, aluminum, and brass. These metals are chosen for their strength and resistance to heat. The sparkwheel and hood, often made from steel, must withstand repeated use without degrading.
Plastic Components
Plastics are equally important in lighter production. They offer flexibility and are lightweight. The BIC lighter incorporates plastics such as acetyl resin or Delrin. These materials are used for the lighter’s body and base. They ensure the lighter remains lightweight yet robust enough to handle daily wear and tear.
Fuel and Ignition Materials
Fuel and ignition materials are at the heart of a lighter’s operation. Most lighters use liquid gas, like butane, which is stored under pressure. This fuel provides a consistent flame. The ignition system often includes a flint, which creates sparks to ignite the gas. This combination ensures the lighter functions reliably every time.
Design Considerations
Designing a lighter involves more than just assembling parts. It requires careful consideration of both safety and aesthetics.
Safety Features
Safety is paramount in lighter design. I have learned that manufacturers incorporate various features to prevent accidents. For example, child-resistant mechanisms are standard in many lighters. These features make it difficult for young children to operate the lighter, reducing the risk of accidental ignition.
Aesthetic and Functional Design
Aesthetic and functional design go hand in hand. Lighters must be visually appealing while remaining practical. Manufacturers often experiment with colors and shapes to attract consumers. However, they also ensure that the design does not compromise the lighter’s usability. The balance between form and function is key to a successful product.
Step-by-Step Manufacturing Process
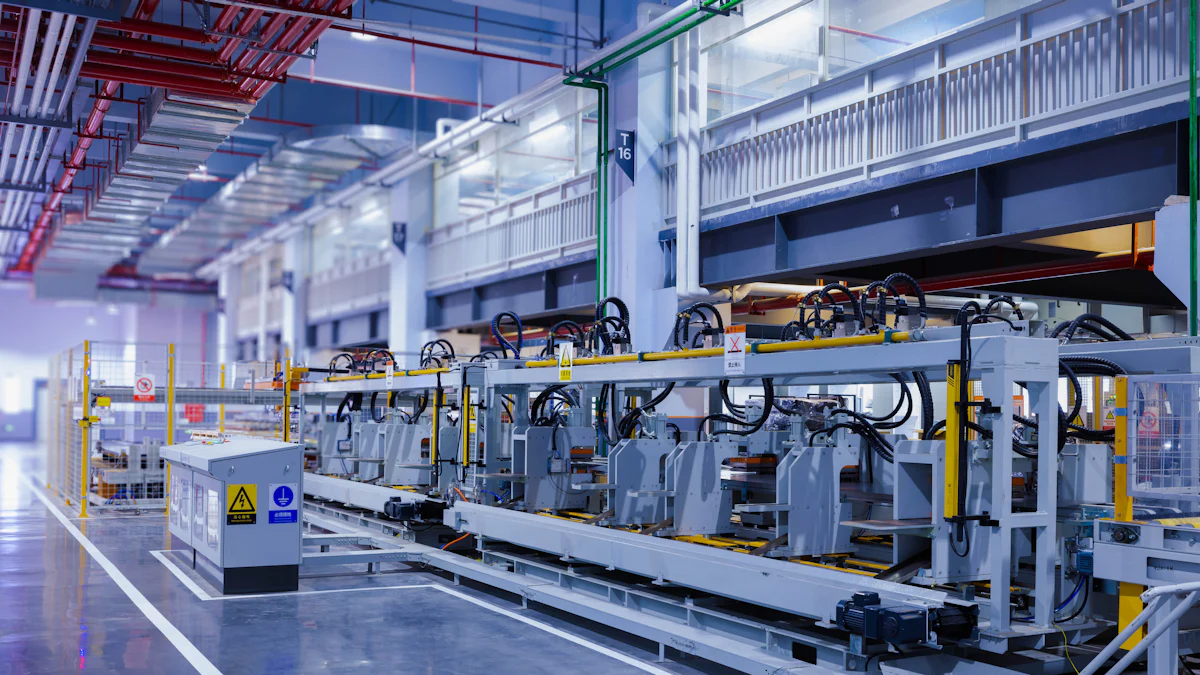
The manufacturing of lighters involves a series of precise steps, each crucial to the final product’s quality and functionality. I find this process fascinating as it combines both traditional techniques and modern technology.
Receiving and Preparing Raw Materials
The journey begins with the arrival of raw materials. I ensure that each batch undergoes thorough inspection to meet quality standards.
Material Inspection
I prioritize material inspection. This step involves checking for defects and verifying the specifications. It ensures that only high-quality materials proceed to the next stage. For instance, metals must be free from impurities, and plastics should have the right consistency.
Storage and Handling
Proper storage and handling are essential. I store materials in controlled environments to prevent degradation. Metals and plastics require specific conditions to maintain their properties. This careful handling preserves the integrity of the materials until they are ready for use.
Component Manufacturing
Once the materials are prepared, I move on to component manufacturing. This stage involves shaping the raw materials into parts that will form the lighter.
Metal Stamping and Molding
Metal stamping and molding are key processes. I use these techniques to create durable metal components. The lighter production machine plays a vital role here. It ensures precision and efficiency, producing parts like the sparkwheel and hood with exact specifications.
Plastic Injection Molding
Plastic injection molding is another critical process. I use it to form the lighter’s body and base. The lighter production machine injects molten plastic into molds, creating components that are both lightweight and strong. This method allows for intricate designs and consistent quality.
Assembly Process
With all components ready, I proceed to the assembly process. This stage brings together the various parts to form a complete lighter.
Automated Assembly Line
The automated assembly line is a marvel of modern engineering. I rely on it to assemble lighters quickly and accurately. The lighter production machine handles tasks like attaching the sparkwheel and filling the fuel tank. This automation increases efficiency and reduces human error.
Manual Assembly for Complex Parts
Despite automation, some parts require manual assembly. I oversee this process for complex components that need a personal touch. Skilled workers ensure that these parts fit perfectly, maintaining the lighter’s functionality and safety.
Final Packaging
The final packaging stage is crucial in the lighter manufacturing process. It ensures that each lighter reaches the consumer in perfect condition. I focus on two main aspects during this stage: packaging design and distribution preparation.
Packaging Design
Packaging design plays a vital role in protecting the product and attracting customers. I prioritize creating packaging that is both functional and visually appealing. The design must safeguard the lighter from damage during transit. I use materials that provide cushioning and support, ensuring the lighter remains intact.
Additionally, the packaging serves as a marketing tool. I incorporate branding elements such as logos and color schemes to make the product stand out on store shelves. The design must also convey important information, like safety instructions and product features, clearly and concisely.
Distribution Preparation
Once the packaging design is finalized, I move on to distribution preparation. This step involves organizing the packaged lighters for shipment. I ensure that each package is labeled correctly with destination details and tracking information. This accuracy minimizes errors and ensures timely delivery.
I also consider the logistics of distribution. Efficient packing methods maximize space and reduce shipping costs. I work closely with logistics partners to streamline the process, ensuring that the lighters reach retailers and consumers promptly.
Incorporating advanced technologies, such as 3D printing, can enhance packaging design. For instance, Scalmalloy, a metal powder alloy, offers lightweight yet strong components. This innovation can improve packaging materials, making them more durable and cost-effective.
Quality Control Measures
Quality control is a vital part of lighter manufacturing. I focus on ensuring that each lighter meets high standards of functionality and safety. This involves a series of inspections and tests, as well as continuous improvement efforts.
Inspection and Testing
I conduct thorough inspections and tests to verify the quality of each lighter. This process ensures that every product functions correctly and safely.
Functional Testing
Functional testing is essential. I test each lighter to ensure it ignites properly and produces a steady flame. This involves checking the ignition mechanism and fuel system. I make sure that the lighter operates smoothly and consistently. This step guarantees that the product performs as expected in everyday use.
Safety Testing
Safety testing is equally important. I prioritize testing for potential hazards. This includes checking for leaks and ensuring that the lighter’s safety features work effectively. For instance, child-resistant mechanisms undergo rigorous testing to confirm their reliability. I adhere to safety standards to protect consumers from accidents.
Continuous Improvement
Continuous improvement is a key aspect of my quality control strategy. I strive to enhance the manufacturing process and product quality through feedback and compliance with standards.
Feedback and Adjustments
Feedback plays a crucial role in continuous improvement. I gather input from customers and industry experts to identify areas for enhancement. This feedback helps me make necessary adjustments to the production process. I focus on refining techniques and materials to improve the overall quality of the lighters.
Compliance with Standards
Compliance with industry standards is non-negotiable. I ensure that all lighters meet regulatory requirements, such as those outlined in the Federal Hazardous Substances Act (FHSA). This involves adhering to guidelines for cautionary labeling and safety features. By maintaining compliance, I uphold the integrity and reputation of the product.
I emphasize the importance of waste management in lighter manufacturing. Efficient waste management reduces environmental impact and enhances sustainability. I focus on recycling materials and minimizing waste during production. This approach not only conserves resources but also aligns with global environmental standards.
Looking ahead, I see exciting trends in lighter production technology. Innovations like smart lighters and eco-friendly materials are gaining traction. These advancements promise to revolutionize the industry. I believe that embracing these technologies will lead to safer, more efficient, and environmentally friendly lighter production.
BIC Group highlights that employees spend nearly 25% of their time ensuring product quality through advanced technologies and over 50 automatic checks. This dedication to quality assurance sets a high standard for future innovations.
FAQ
What materials are commonly used in lighter manufacturing?
I use a combination of metals and plastics in lighter manufacturing. Metals like steel, aluminum, and brass provide durability and structural integrity. Plastics such as acetyl resin or Delrin offer flexibility and lightweight properties. These materials ensure the lighter’s functionality and safety.
How does the lighter production machine enhance efficiency?
The lighter production machine automates various processes, increasing efficiency and consistency. It reduces labor costs by handling tasks like metal stamping, plastic injection molding, and assembly. This automation allows for the production of millions of lighters daily, ensuring high throughput and quality.
What are the environmental impacts of disposable lighters?
Disposable lighters contribute significantly to environmental pollution. They generate more waste and plastic pollution compared to refillable lighters. The accumulation of disposable lighters in landfills poses long-term environmental challenges. I recommend using refillable lighters to reduce waste and lower the carbon footprint.
How do safety features in lighters work?
Safety features in lighters prevent accidents and ensure user safety. Child-resistant mechanisms make it difficult for young children to operate the lighter. These features undergo rigorous testing to confirm their reliability. I prioritize incorporating these safety measures in all lighter designs.
What is the difference between BIC lighters and other brands?
BIC lighters are known for their durability and reliability. However, they are difficult to refill and recycle, leading to increased waste in landfills. While brass components in BIC lighters are recyclable, they can still contribute to environmental issues. Other brands may offer more eco-friendly options.
How does packaging design impact lighter manufacturing?
Packaging design plays a crucial role in protecting the product and attracting customers. I focus on creating packaging that is both functional and visually appealing. Lightweight packaging solutions result in less waste creation and reduced expenses compared to traditional packaging. This approach aligns with sustainability goals.
Why is quality control important in lighter manufacturing?
Quality control ensures that each lighter meets high standards of functionality and safety. I conduct thorough inspections and tests to verify the quality of every product. This process guarantees that the lighter operates smoothly and safely, protecting consumers from potential hazards.
How do refillable lighters benefit the environment?
Refillable lighters offer several environmental benefits. They generate less waste and reduce plastic pollution compared to disposable lighters. By using refillable lighters, I help lower the carbon footprint and promote sustainability. This choice aligns with global efforts to conserve resources and protect the environment.
What future trends are emerging in lighter production technology?
Innovations like smart lighters and eco-friendly materials are gaining traction in the industry. These advancements promise to revolutionize lighter production. I believe embracing these technologies will lead to safer, more efficient, and environmentally friendly lighter manufacturing.