Master the J0-GZ-3VCP semi-automatic aerosol machine
The J0-GZ-3VCP (three-in-one) semi-automatic aerosol filling machine offers a reliable solution for efficient aerosol production. You can use this machine to streamline the process of liquid filling, crimping, and gas filling. Its design ensures precision and reduces manual effort, making it ideal for medium to high production needs. By mastering its setup and operation, you can achieve consistent results while maintaining safety. This machine empowers you to handle aerosol production with confidence and efficiency, whether you are new to the process or looking to enhance your current workflow.
Key Takeaways
- The J0-GZ-3VCP machine combines liquid filling, crimping, and gas filling, making it a versatile solution for aerosol production.
- Proper assembly and setup of the machine are crucial for smooth operation; follow the user manual for detailed instructions.
- Safety is paramount: always wear appropriate personal protective equipment (PPE) and ensure proper ventilation in the workspace.
- Regular cleaning and maintenance of the machine enhance its efficiency and longevity, preventing operational issues.
- Monitor the filling process closely to ensure accuracy and consistency in product quality.
- Establish clear emergency procedures to respond effectively to unexpected situations, ensuring the safety of all operators.
- Document production runs to track efficiency and identify areas for improvement, contributing to better workflow management.
Overview of the J0-GZ-3VCP (three-in-one) semi-automatic aerosol filling machine
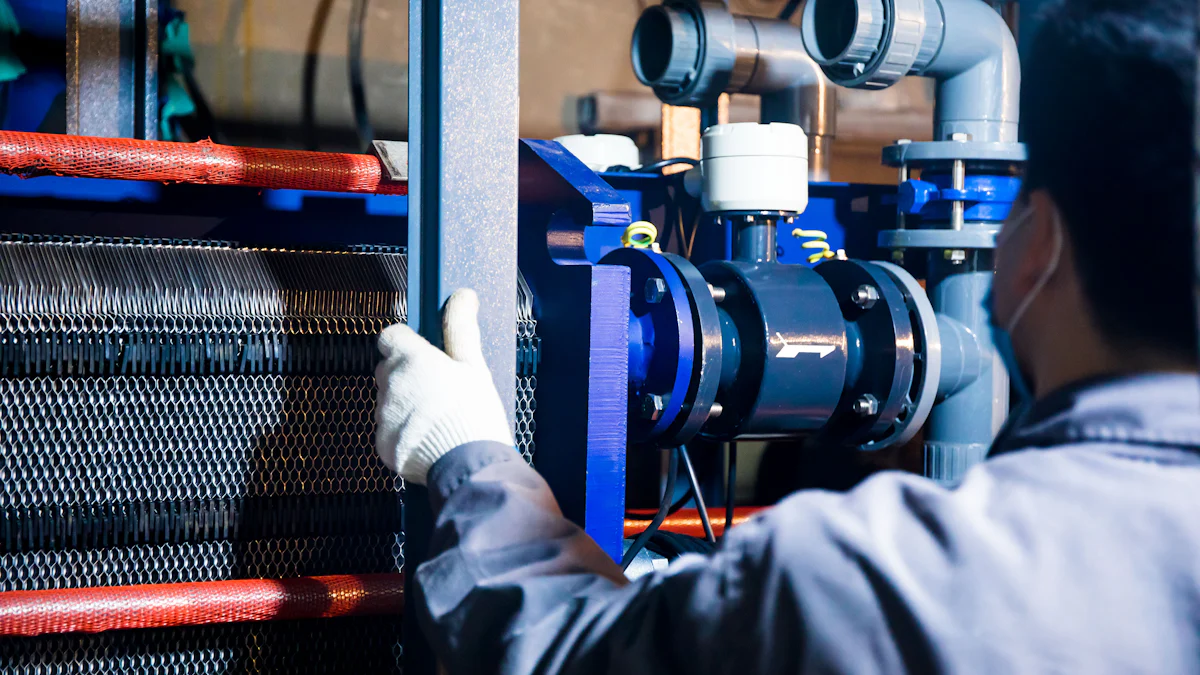
The J0-GZ-3VCP (three-in-one) semi-automatic aerosol filling machine serves as a versatile tool for aerosol production. You can use it to streamline the processes of liquid filling, crimping, and gas filling. This machine is ideal for industries that produce aerosol products such as deodorants, air fresheners, lubricants, and spray paints. Its design supports medium to high production needs, making it suitable for small businesses and large-scale manufacturers alike. By incorporating this machine into your workflow, you can achieve faster production rates and consistent product quality.
Key Features
This machine offers several features that enhance its efficiency and usability. First, it combines three essential functions—liquid filling, crimping, and gas filling—into one compact unit. This integration reduces the need for multiple machines and simplifies the production process. Second, it supports a wide range of can sizes, accommodating diameters from 35mm to 65mm and heights from 80mm to 350mm. This flexibility allows you to handle various product types without frequent adjustments.
Additionally, the machine can fill between 3,000 to 5,000 cans in an 8-hour shift. This high output capacity ensures that you can meet demanding production schedules. The user-friendly interface and semi-automatic operation make it easy to use, even for operators with minimal experience. Safety features, such as a guiding filling plate for accurate alignment and mechanisms to handle flammable propellants, further enhance its reliability.
Main Components
The J0-GZ-3VCP (three-in-one) semi-automatic aerosol filling machine consists of several key components that work together seamlessly. The liquid filling system ensures precise measurement and dispensing of liquids into the cans. The crimping mechanism securely seals the cans, preventing leaks and maintaining product integrity. The gas filling system injects the required propellant, completing the aerosol production process.
The machine also includes a guiding filling plate, which aligns the cans for accurate filling and sealing. A foot valve activates the sealing mechanism, allowing you to control the process with ease. The power supply system ensures consistent performance, while the durable frame provides stability during operation. Each component is designed to maximize efficiency and minimize downtime, ensuring smooth production.
Pre-Operation Setup
Assembling the Machine
Proper assembly of the J0-GZ-3VCP semi-automatic aerosol filling machine is essential for smooth operation. Start by unpacking all components and inspecting them for any visible damage. Lay out the parts in an organized manner to ensure nothing is missing. Refer to the user manual for a detailed diagram of the machine’s structure.
Follow these steps to assemble the machine:
- Attach the Main Components: Secure the liquid filling system, crimping mechanism, and gas filling system to their designated positions on the machine frame. Use the provided tools to tighten bolts and screws.
- Install the Guiding Filling Plate: Align the guiding filling plate with the filling platform. This ensures accurate positioning of the aerosol cans during operation.
- Connect the Foot Valve: Attach the foot valve to the sealing mechanism. This allows you to control the sealing process with precision.
- Check All Connections: Inspect all connections, including hoses and wires, to confirm they are secure and properly aligned.
Take your time during assembly to avoid errors. A well-assembled machine minimizes operational issues and ensures consistent performance.
Checking the Power Supply
A reliable power supply is critical for the machine’s operation. Before connecting the machine to a power source, verify the voltage requirements specified in the user manual. Most models operate on standard industrial power supplies.
Here’s how to check the power supply:
- Inspect the Power Cord: Look for any signs of wear or damage. Replace the cord if necessary to prevent electrical hazards.
- Test the Outlet: Use a voltage tester to confirm that the outlet provides the correct voltage. Avoid using outlets with fluctuating power levels.
- Connect the Machine: Plug the machine into the outlet and switch it on briefly to ensure it powers up correctly. Turn it off immediately after testing.
Always prioritize safety when working with electrical components. If you encounter any issues, consult a qualified technician before proceeding.
Preparing the Work Area
Setting up a clean and organized work area enhances efficiency and safety. Choose a location that meets the machine’s operational requirements and provides ample space for movement.
Follow these guidelines to prepare your workspace:
- Clear the Area: Remove any unnecessary items or debris from the work surface. A clutter-free environment reduces the risk of accidents.
- Ensure Proper Ventilation: Aerosol production involves handling flammable materials. Good ventilation prevents the buildup of harmful fumes.
- Position the Machine: Place the machine on a stable, level surface. This prevents vibrations and ensures accurate filling and sealing.
- Organize Tools and Materials: Arrange all tools, cans, and raw materials within easy reach. This streamlines the workflow and minimizes downtime.
A well-prepared work area not only improves productivity but also ensures compliance with safety standards. Take the time to set up your space correctly before starting operations.
Safety Preparations
Ensuring safety is a critical step before operating the J0-GZ-3VCP semi-automatic aerosol filling machine. Proper precautions protect you and your team from potential hazards while maintaining a smooth workflow. Follow these essential safety preparations to create a secure working environment.
1. Wear Appropriate Personal Protective Equipment (PPE)
Protective gear minimizes exposure to harmful substances and reduces the risk of injury. Equip yourself with the following:
- Safety Goggles: Shield your eyes from liquid splashes or gas emissions.
- Gloves: Use chemical-resistant gloves to handle materials safely.
- Protective Clothing: Wear long-sleeved garments and aprons to prevent skin contact with chemicals.
- Respiratory Mask: Use a mask to avoid inhaling fumes, especially when working with flammable propellants.
Inspect your PPE for damage before use. Replace any worn or defective items immediately.
2. Inspect the Machine for Safety Hazards
A thorough inspection ensures the machine operates safely. Check for the following:
- Loose Components: Tighten any bolts, screws, or connections that appear loose.
- Damaged Parts: Look for cracks, leaks, or wear in the machine’s components.
- Electrical Safety: Confirm that wires and cables are intact and properly insulated.
Address any issues before starting the machine. Operating a faulty machine increases the risk of accidents.
3. Handle Aerosol Materials with Care
Aerosol production involves handling flammable and pressurized materials. Follow these guidelines to ensure safe material handling:
- Store Materials Properly: Keep liquids and propellants in labeled, sealed containers. Store them in a cool, dry place away from heat sources.
- Avoid Spills: Use funnels or dispensers to transfer liquids without spilling. Clean up any spills immediately to prevent slips or chemical reactions.
- Check Material Compatibility: Verify that the materials you use are compatible with the machine’s specifications.
Handling materials responsibly reduces the likelihood of accidents and ensures consistent product quality.
4. Establish Emergency Procedures
Prepare for unexpected situations by setting up clear emergency protocols. Include the following in your plan:
- Fire Safety: Keep fire extinguishers nearby and ensure all workers know how to use them.
- First Aid: Stock a first aid kit in the work area. Train team members to respond to common injuries.
- Evacuation Plan: Designate exit routes and assembly points in case of emergencies.
Review these procedures regularly with your team. Being prepared can save lives and minimize damage during emergencies.
5. Ensure Proper Ventilation
Good ventilation prevents the buildup of harmful fumes and reduces fire risks. Set up your workspace with these considerations:
- Install Exhaust Fans: Use fans to remove fumes from the area.
- Open Windows or Doors: Allow fresh air to circulate freely.
- Monitor Air Quality: Use detectors to measure gas levels and ensure a safe environment.
A well-ventilated workspace protects your health and enhances overall safety.
By following these safety preparations, you can create a secure and efficient environment for operating the J0-GZ-3VCP semi-automatic aerosol filling machine. Prioritizing safety not only protects you but also ensures the longevity of your equipment and the quality of your products.
Step-by-Step Operation Guide
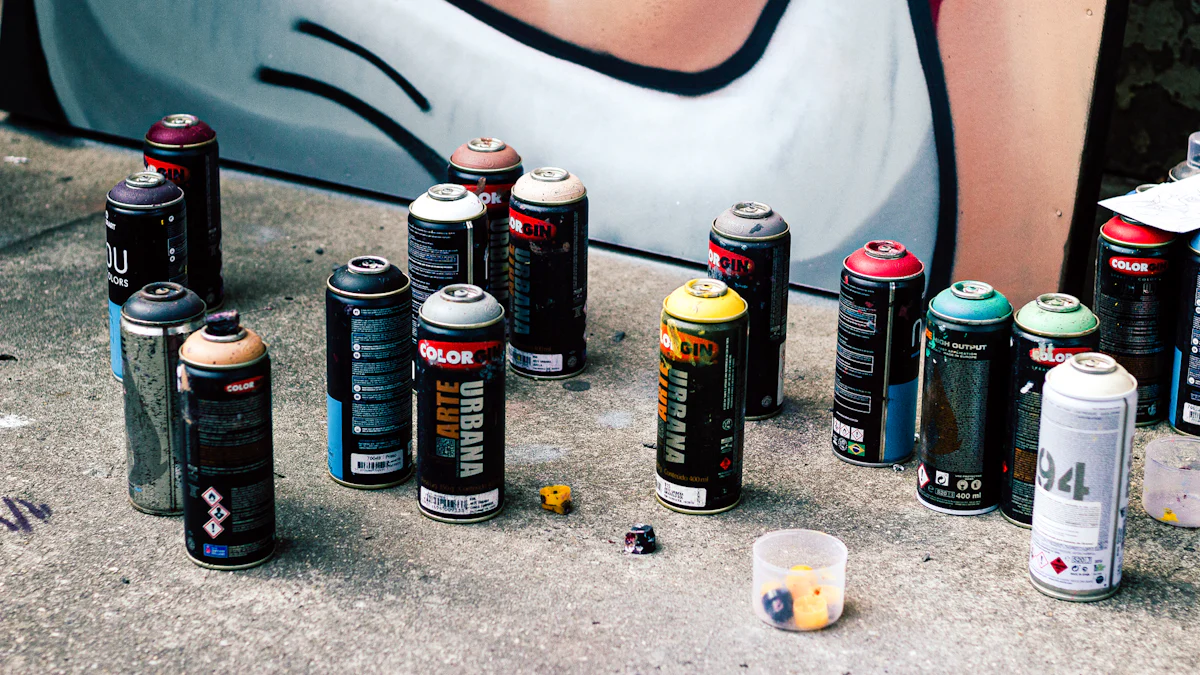
Loading Materials
Loading materials into the J0-GZ-3VCP (three-in-one) semi-automatic aerosol filling machine is the first step in the operation process. Begin by preparing the materials you will use, such as the liquid product, propellant, and empty aerosol cans. Ensure that all materials meet the specifications outlined in the machine’s user manual.
Follow these steps to load materials:
- Position the Aerosol Cans: Place the empty cans onto the guiding filling plate. Align them properly to ensure accurate filling during the process.
- Prepare the Liquid Product: Pour the liquid product into the designated reservoir of the machine. Avoid overfilling the reservoir to prevent spillage.
- Set Up the Propellant: Connect the propellant container to the gas filling system. Check that the connection is secure and free from leaks.
- Inspect the Materials: Verify that the cans, liquid, and propellant are compatible with the machine’s settings. This step ensures smooth operation and prevents damage to the equipment.
By carefully loading the materials, you set the foundation for a successful filling process. Take your time to double-check each step before proceeding.
Starting the Filling Process
Once the materials are loaded, you can begin the filling process. This step involves transferring the liquid product into the aerosol cans with precision and efficiency.
Here’s how to start the filling process:
- Activate the Machine: Turn on the power supply and ensure the machine is functioning correctly. Check the control panel for any error messages or warnings.
- Adjust the Settings: Use the control interface to set the desired filling volume. Refer to the product specifications to determine the correct amount for each can.
- Initiate the Filling: Push the aerosol can into the guiding filling plate. The machine will automatically align the can and dispense the liquid product into it.
- Monitor the Process: Observe the filling process to ensure accuracy. If you notice any irregularities, pause the operation and inspect the machine for issues.
Starting the filling process requires attention to detail. By monitoring the operation closely, you can maintain consistent product quality and avoid errors.
Sealing and Crimping
Sealing and crimping are critical steps in aerosol production. These processes secure the contents of the can and prepare it for the final gas filling stage.
To seal and crimp the cans, follow these steps:
- Position the Can: After filling, move the can to the sealing mechanism. Ensure it is properly aligned with the crimping tool.
- Engage the Sealing Mechanism: Open the sealing rotary switch and press the foot valve. This action activates the crimping tool, which securely seals the can.
- Inspect the Seal: Check the crimped can for any signs of leakage or improper sealing. A well-sealed can should have a uniform crimp around the edge.
- Repeat the Process: Continue sealing and crimping the remaining cans. Maintain a steady workflow to ensure efficiency.
Proper sealing and crimping protect the integrity of the product and prevent leaks. Take care to inspect each can before moving on to the next step.
By following this step-by-step guide, you can operate the J0-GZ-3VCP (three-in-one) semi-automatic aerosol filling machine effectively. Each step plays a vital role in ensuring the quality and safety of your aerosol products. Practice these procedures regularly to build confidence and improve your production efficiency.
Final Steps
Completing the aerosol production process with the J0-GZ-3VCP semi-automatic aerosol filling machine requires careful attention to detail. The final steps ensure that your products meet quality standards and are ready for distribution. Follow these steps to wrap up the operation effectively:
-
Perform a Quality Check
Inspect each filled and sealed aerosol can for defects. Look for issues such as leaks, uneven crimping, or incorrect filling levels. Remove any defective cans from the batch to maintain product consistency. A thorough quality check ensures customer satisfaction and prevents potential safety hazards. -
Label and Package the Cans
Apply labels to the aerosol cans according to your product specifications. Ensure that the labels are aligned and securely attached. Once labeled, organize the cans into appropriate packaging, such as cartons or trays. Proper packaging protects the cans during transportation and storage. -
Clean the Machine
Turn off the machine and disconnect it from the power supply. Use a clean cloth and appropriate cleaning agents to wipe down the liquid filling system, crimping mechanism, and gas filling system. Remove any residue or spills to prevent contamination during future operations. Regular cleaning extends the machine’s lifespan and ensures optimal performance. -
Store Materials Safely
Return unused materials, such as liquids and propellants, to their designated storage areas. Seal the containers tightly and label them clearly. Store them in a cool, dry place away from heat sources or open flames. Proper storage minimizes waste and reduces the risk of accidents. -
Document the Production Process
Record details of the production run, including the number of cans filled, materials used, and any issues encountered. Maintain these records for future reference and compliance with industry regulations. Documentation helps you track production efficiency and identify areas for improvement. -
Prepare for the Next Operation
Check the machine for wear or damage. Replace any worn-out parts to avoid disruptions during the next production cycle. Organize tools and materials for easy access. A well-prepared setup saves time and ensures a smooth start for the next operation.
“Efficiency is doing things right; effectiveness is doing the right things.” – Peter Drucker. By following these final steps, you ensure both efficiency and effectiveness in your aerosol production process.
Completing these steps with care guarantees high-quality products and a safe working environment. Consistency in your approach builds trust with your customers and enhances your production capabilities.
Safety Guidelines
General Safety Tips
Operating the J0-GZ-3VCP semi-automatic aerosol filling machine requires strict adherence to safety practices. Following these general safety tips will help you maintain a secure working environment and prevent accidents.
- Stay Focused During Operation: Always pay attention to the task at hand. Avoid distractions, such as using your phone or engaging in unrelated conversations, while operating the machine. Staying alert reduces the risk of errors.
- Inspect Equipment Regularly: Check the machine for wear, damage, or loose components before each use. Address any issues immediately to avoid malfunctions during operation.
- Keep the Work Area Clean: Maintain a clutter-free workspace. Remove unnecessary tools, materials, or debris that could cause tripping hazards or interfere with the machine’s operation.
- Follow Manufacturer Instructions: Refer to the user manual for guidance on operating and maintaining the machine. Adhering to the manufacturer’s recommendations ensures safe and efficient use.
- Avoid Overloading the Machine: Operate the machine within its specified capacity. Overloading can lead to equipment failure or compromised product quality.
By incorporating these tips into your routine, you can create a safer and more productive work environment.
Handling Aerosol Materials
Aerosol production involves working with pressurized and flammable substances. Proper handling of these materials is essential to ensure safety and maintain product quality.
- Store Materials Correctly: Keep liquids and propellants in labeled, sealed containers. Store them in a cool, dry location away from heat sources or open flames.
- Use Appropriate Tools: Employ funnels, dispensers, or other tools to transfer liquids and propellants. This minimizes spills and reduces the risk of exposure to harmful substances.
- Avoid Mixing Incompatible Materials: Verify that the materials you use are compatible with the machine’s specifications. Mixing incompatible substances can result in chemical reactions or equipment damage.
- Handle Pressurized Containers with Care: Treat pressurized containers gently to prevent punctures or leaks. Avoid dropping or mishandling them during storage or use.
- Dispose of Waste Properly: Follow local regulations for disposing of unused materials or empty containers. Improper disposal can harm the environment and pose safety risks.
Handling aerosol materials responsibly protects both you and the environment while ensuring consistent production results.
Emergency Procedures
Preparing for emergencies is a critical aspect of operating the J0-GZ-3VCP semi-automatic aerosol filling machine. Establishing clear procedures will help you respond effectively to unexpected situations.
-
Identify Potential Hazards
Familiarize yourself with the risks associated with aerosol production, such as fires, chemical spills, or equipment malfunctions. Understanding these hazards allows you to act quickly when needed. -
Keep Fire Safety Equipment Nearby
Place fire extinguishers in accessible locations within the work area. Ensure they are suitable for flammable materials and train all team members on their proper use. -
Develop an Evacuation Plan
Create a clear evacuation plan that includes exit routes and assembly points. Share this plan with your team and conduct regular drills to ensure everyone knows what to do in an emergency. -
Stock a First Aid Kit
Equip your workspace with a well-stocked first aid kit. Include supplies for treating burns, cuts, or chemical exposure. Train team members to provide basic first aid when necessary. -
Respond to Spills Immediately
Clean up spills promptly using appropriate materials, such as absorbent pads or neutralizing agents. Wear protective gear to avoid contact with hazardous substances. -
Shut Down the Machine Safely
In case of equipment failure or other emergencies, turn off the machine and disconnect it from the power supply. This prevents further damage and ensures the safety of everyone in the area.
“Preparedness is the key to safety.” By implementing these emergency procedures, you can minimize risks and protect both your team and your equipment during unforeseen events.
Maintenance and Troubleshooting
Cleaning the Machine
Keeping the J0-GZ-3VCP semi-automatic aerosol filling machine clean ensures its efficiency and longevity. Regular cleaning prevents residue buildup, which can affect performance and compromise product quality. Follow these steps to clean the machine effectively:
-
Turn Off the Machine
Disconnect the machine from the power supply before cleaning. This step eliminates the risk of electrical accidents and ensures your safety. -
Wipe Down External Surfaces
Use a soft, damp cloth to clean the exterior of the machine. Remove dust, spills, or any visible dirt. Avoid using abrasive materials that could damage the surface. -
Clean the Liquid Filling System
Flush the liquid filling system with a cleaning solution compatible with the materials you use. This step removes any leftover product and prevents contamination during the next operation. -
Inspect and Clean the Crimping Mechanism
Check the crimping tool for residue or debris. Use a small brush or cloth to clean it thoroughly. Ensure the tool remains free of obstructions for accurate sealing. -
Maintain the Gas Filling System
Detach the gas filling components and clean them carefully. Inspect for leaks or blockages. Reassemble the parts securely after cleaning. -
Dry All Components
Allow all cleaned parts to air dry completely before reassembling the machine. Moisture can lead to corrosion or affect the machine’s functionality.
“A clean machine is a reliable machine.” By dedicating time to proper cleaning, you ensure consistent performance and extend the life of your equipment.
Regular Maintenance
Routine maintenance keeps the J0-GZ-3VCP machine running smoothly and minimizes downtime. Performing regular checks helps you identify potential issues early. Incorporate these maintenance tasks into your schedule:
-
Inspect Moving Parts
Examine all moving components, such as the guiding filling plate and foot valve. Look for signs of wear or misalignment. Replace worn-out parts promptly to avoid operational disruptions. -
Lubricate Key Mechanisms
Apply lubricant to the machine’s moving parts as recommended in the user manual. Proper lubrication reduces friction and prevents premature wear. -
Check Electrical Connections
Inspect wires and cables for damage or loose connections. Secure any loose wires and replace damaged ones to maintain electrical safety. -
Test the Sealing Mechanism
Operate the crimping tool without materials to ensure it functions correctly. Adjust the settings if necessary to maintain precision. -
Verify Calibration
Confirm that the machine’s settings, such as filling volume and pressure, remain accurate. Recalibrate the machine periodically to ensure consistent results. -
Replace Filters
If the machine uses filters for the gas filling system, replace them according to the manufacturer’s guidelines. Clean filters improve performance and prevent clogs.
By performing these maintenance tasks regularly, you reduce the likelihood of unexpected breakdowns and maintain optimal production efficiency.
Troubleshooting Common Issues
Even with proper care, you may encounter occasional issues while operating the J0-GZ-3VCP machine. Knowing how to troubleshoot common problems helps you resolve them quickly and resume production. Here are some typical issues and their solutions:
-
Inconsistent Filling Volumes
- Cause: Blockages in the liquid filling system or incorrect calibration.
- Solution: Clean the filling system thoroughly. Recalibrate the machine to match the desired filling volume.
-
Leaking Seals
- Cause: Misaligned cans or a worn crimping tool.
- Solution: Realign the cans on the guiding filling plate. Inspect the crimping tool and replace it if necessary.
-
Gas Filling Malfunctions
- Cause: Loose connections or depleted propellant supply.
- Solution: Tighten all connections in the gas filling system. Check the propellant container and replace it if empty.
-
Machine Fails to Start
- Cause: Electrical issues or a faulty power supply.
- Solution: Inspect the power cord and outlet. Replace damaged components or consult a technician if the issue persists.
-
Unusual Noises During Operation
- Cause: Lack of lubrication or loose parts.
- Solution: Lubricate moving components and tighten any loose screws or bolts.
-
Overheating
- Cause: Prolonged use without breaks or inadequate ventilation.
- Solution: Allow the machine to cool down before resuming operation. Improve ventilation in the workspace to prevent overheating.
“Every problem has a solution.” By understanding these common issues and their fixes, you can minimize downtime and keep your production line running efficiently.
Regular cleaning, maintenance, and troubleshooting ensure the J0-GZ-3VCP machine operates at its best. By staying proactive, you save time, reduce costs, and maintain high-quality production standards.
The J0-GZ-3VCP (three-in-one) semi-automatic aerosol filling machine provides a dependable solution for efficient aerosol production. By applying the steps in this guide, you enhance your operational skills and ensure consistent results. Regular maintenance and adherence to safety protocols protect both you and the machine. This approach not only improves productivity but also extends the equipment’s lifespan. Mastering this machine empowers you to produce high-quality aerosol products with confidence and precision.
FAQ
What is the J0-GZ-3VCP semi-automatic aerosol filling machine used for?
The J0-GZ-3VCP machine is designed for aerosol production. It combines liquid filling, crimping, and gas filling into one unit. You can use it to manufacture products like deodorants, air fresheners, lubricants, and spray paints. Its versatility makes it suitable for both small businesses and large-scale operations.
How many cans can the machine fill in a day?
The machine can fill between 3,000 to 5,000 cans during an 8-hour shift. This output depends on factors like operator efficiency, material preparation, and proper machine setup. By optimizing your workflow, you can achieve maximum productivity.
What sizes of aerosol cans does the machine support?
The J0-GZ-3VCP accommodates cans with diameters ranging from 35mm to 65mm and heights between 80mm and 350mm. This flexibility allows you to produce a variety of aerosol products without frequent adjustments.
Is the machine easy to operate for beginners?
Yes, the machine features a user-friendly interface and semi-automatic operation. Even if you have minimal experience, you can quickly learn to operate it by following the user manual and this guide. Practicing the steps regularly will help you gain confidence.
What safety precautions should I follow when using the machine?
You should always wear personal protective equipment (PPE), such as safety goggles, gloves, and a respiratory mask. Inspect the machine for loose or damaged parts before starting. Ensure proper ventilation in your workspace to prevent the buildup of harmful fumes. Handling flammable materials with care is also essential.
How often should I clean and maintain the machine?
You should clean the machine after every production run to remove residue and prevent contamination. Perform routine maintenance, such as lubricating moving parts and inspecting electrical connections, at least once a week. Regular upkeep ensures consistent performance and extends the machine’s lifespan.
What should I do if the machine stops working?
If the machine fails to start or stops unexpectedly, check the power supply and electrical connections first. Inspect for loose wires or damaged components. If the issue persists, consult a qualified technician or refer to the troubleshooting section of the user manual.
Can I use the machine with any type of liquid or propellant?
No, you must ensure that the liquids and propellants you use are compatible with the machine’s specifications. Using incompatible materials can damage the equipment or compromise product quality. Always refer to the user manual for guidance on approved materials.
How do I ensure consistent filling accuracy?
To maintain consistent filling accuracy, calibrate the machine regularly. Clean the liquid filling system to prevent blockages. Align the aerosol cans properly on the guiding filling plate. Monitoring the process closely during operation also helps you identify and correct any irregularities.
What should I do in case of an emergency?
In an emergency, turn off the machine and disconnect it from the power supply. Use fire extinguishers for fires and clean up spills immediately using appropriate materials. Follow your workplace’s evacuation plan if necessary. Keeping a first aid kit nearby and training your team on emergency procedures ensures quick and effective responses.
“Preparation and knowledge are your best tools for safety.” By following these FAQs, you can operate the J0-GZ-3VCP machine efficiently and confidently.