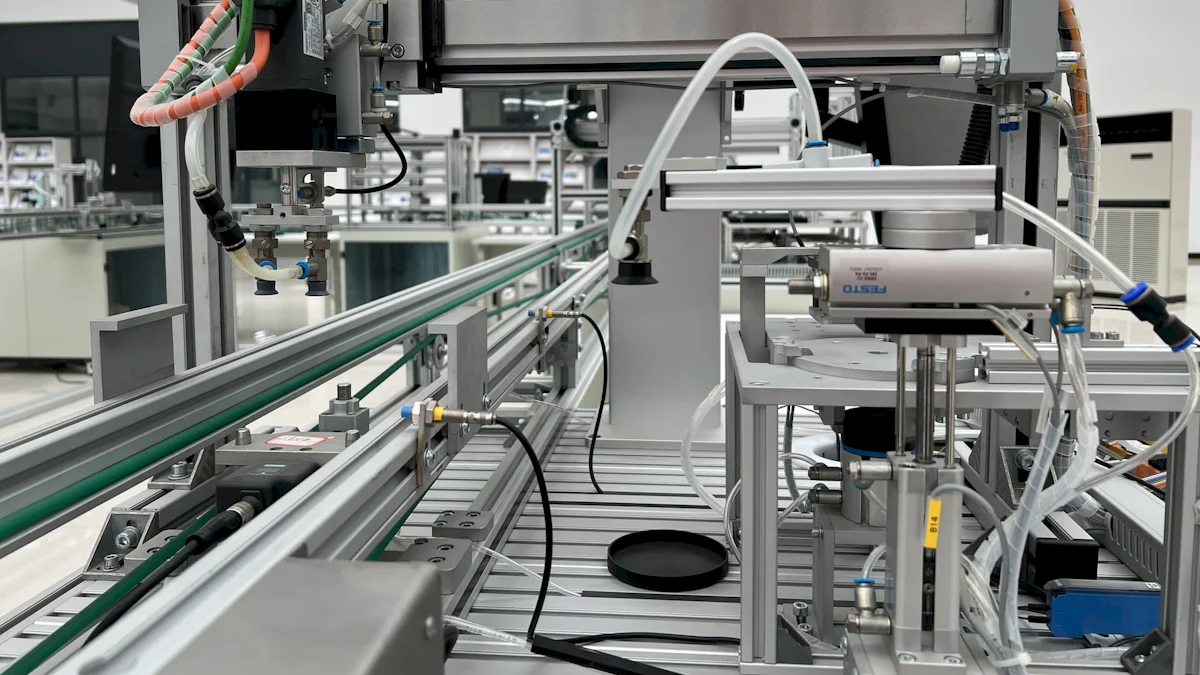
Efficiency plays a crucial role in lighter production lines. You can achieve significant cost savings and boost output by enhancing efficiency. This improvement not only reduces waste but also optimizes the use of resources. Adopting data-driven approaches allows you to make informed decisions, leading to continuous improvement. By focusing on these strategies, you ensure that your lighter production equipment operates at its best, maximizing productivity and profitability.
Key Takeaways
- Implement robust quality control measures to identify defects early and reduce waste, ensuring high product quality.
- Train employees regularly on best practices to enhance their skills and minimize downtime, fostering a culture of continuous improvement.
- Utilize advanced technology, such as automated inspection systems, to improve defect detection and ensure real-time monitoring of production.
- Leverage data analysis to gain insights into production processes, identify inefficiencies, and make informed decisions for optimization.
- Map out production processes to identify bottlenecks and streamline workflows, eliminating unnecessary actions that do not add value.
- Adopt lean manufacturing principles to reduce waste and enhance efficiency, encouraging team participation in identifying and solving issues.
- Provide ongoing training programs to upskill your workforce, ensuring they are equipped with the latest knowledge and techniques for optimal performance.
Optimize First Time Yield in Lighter Production Equipment
Improving the first time yield in lighter production equipment is essential for maximizing efficiency. You can achieve this by focusing on two main strategies: implementing quality control measures and training employees on best practices.
Implement Quality Control Measures
Quality control measures play a vital role in ensuring that your lighter production equipment operates smoothly. By establishing a robust quality control system, you can identify defects early in the production process. This proactive approach helps you reduce waste and improve product quality. Regular inspections and testing should be part of your routine. These practices ensure that each lighter meets the required standards before it leaves the production line. Additionally, using statistical process control tools can help you monitor production trends and make necessary adjustments promptly.
Train Employees on Best Practices
Training your employees on best practices is crucial for optimizing the performance of lighter production equipment. Well-trained employees understand the importance of following standard operating procedures. They can quickly identify and address potential issues, minimizing downtime. Regular training sessions keep your team updated on the latest techniques and technologies. Encourage your employees to provide feedback and share their insights. This collaborative approach fosters a culture of continuous improvement, leading to better efficiency and productivity.
Enhance Defect Detection in Lighter Production Equipment
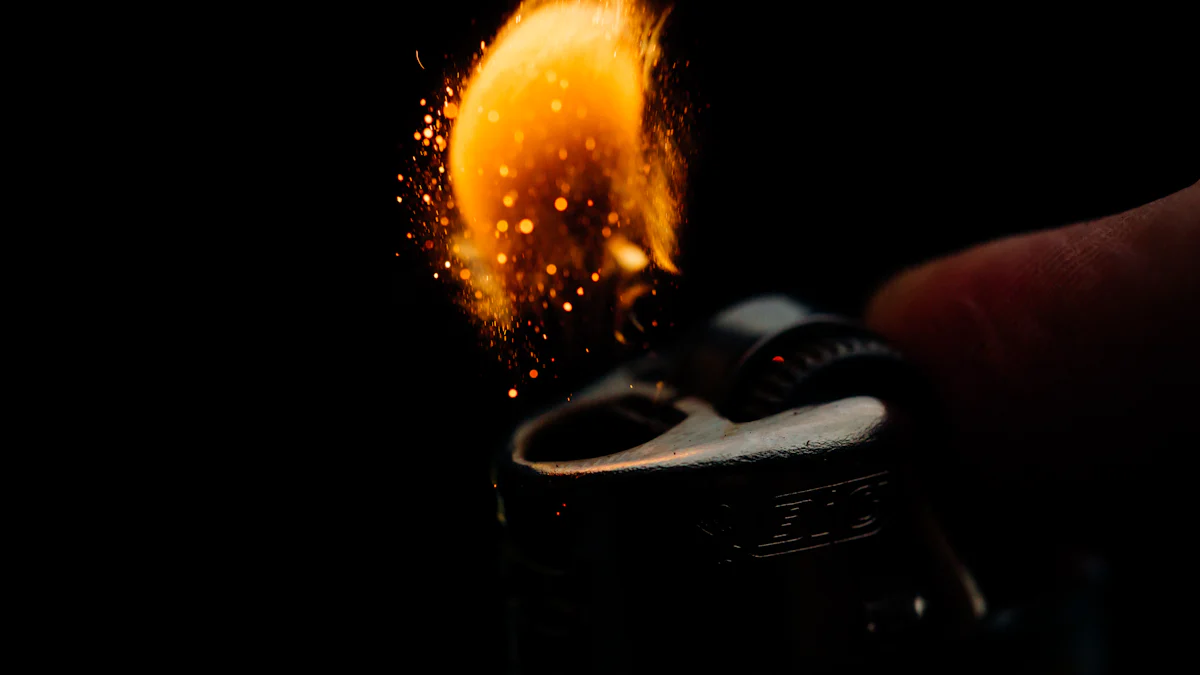
Detecting defects early in the production process is crucial for maintaining the efficiency of lighter production equipment. By focusing on advanced technology and root cause analysis, you can significantly improve defect detection.
Utilize Advanced Technology
Advanced technology plays a pivotal role in enhancing defect detection. You should invest in state-of-the-art inspection systems that can identify defects with high precision. Automated vision systems, for instance, can quickly scan products and detect anomalies that might be missed by the human eye. These systems not only increase the speed of inspections but also improve accuracy. Additionally, integrating sensors and IoT devices into your production line allows for real-time monitoring. This technology provides immediate feedback, enabling you to address issues as they arise. By leveraging these tools, you ensure that your lighter production equipment operates efficiently and produces high-quality products.
Conduct Root Cause Analysis
Root cause analysis is essential for understanding why defects occur. When you identify a defect, it’s important to investigate its origin. This process involves examining the production line and gathering data to pinpoint the underlying cause. Once you understand the root cause, you can implement corrective actions to prevent recurrence. Encourage your team to participate in this analysis. Their insights can be invaluable in identifying potential issues and developing solutions. By fostering a culture of problem-solving, you enhance the overall efficiency of your lighter production equipment. Regularly conducting root cause analysis helps you maintain high standards and reduce waste.
Leverage Data Analysis for Lighter Production Equipment
Data analysis plays a crucial role in enhancing the efficiency of lighter production equipment. By leveraging data, you can gain valuable insights into your production processes and make informed decisions to optimize performance.
Implement Data Collection Systems
To effectively analyze data, you must first implement robust data collection systems. These systems gather information from various stages of the production line. Sensors and IoT devices can capture real-time data on machine performance, production rates, and quality metrics. By collecting this data, you create a comprehensive overview of your operations. This information serves as the foundation for identifying trends and patterns that impact efficiency. Ensure that your data collection systems are reliable and capable of handling large volumes of data. Regularly calibrate and maintain these systems to ensure accuracy and consistency.
Analyze Data for Insights
Once you have collected data, the next step is to analyze it for actionable insights. Use data analytics tools to process and interpret the information. Look for patterns that indicate inefficiencies or areas for improvement. For example, you might discover that certain machines consistently underperform during specific shifts. By identifying these issues, you can take corrective actions to enhance efficiency. Share your findings with your team and involve them in developing solutions. Encourage a data-driven culture where decisions are based on evidence rather than assumptions. Regularly review and update your analysis to keep pace with changes in production dynamics. By doing so, you ensure that your lighter production equipment operates at peak efficiency.
Streamline Workflow Efficiency in Lighter Production Equipment
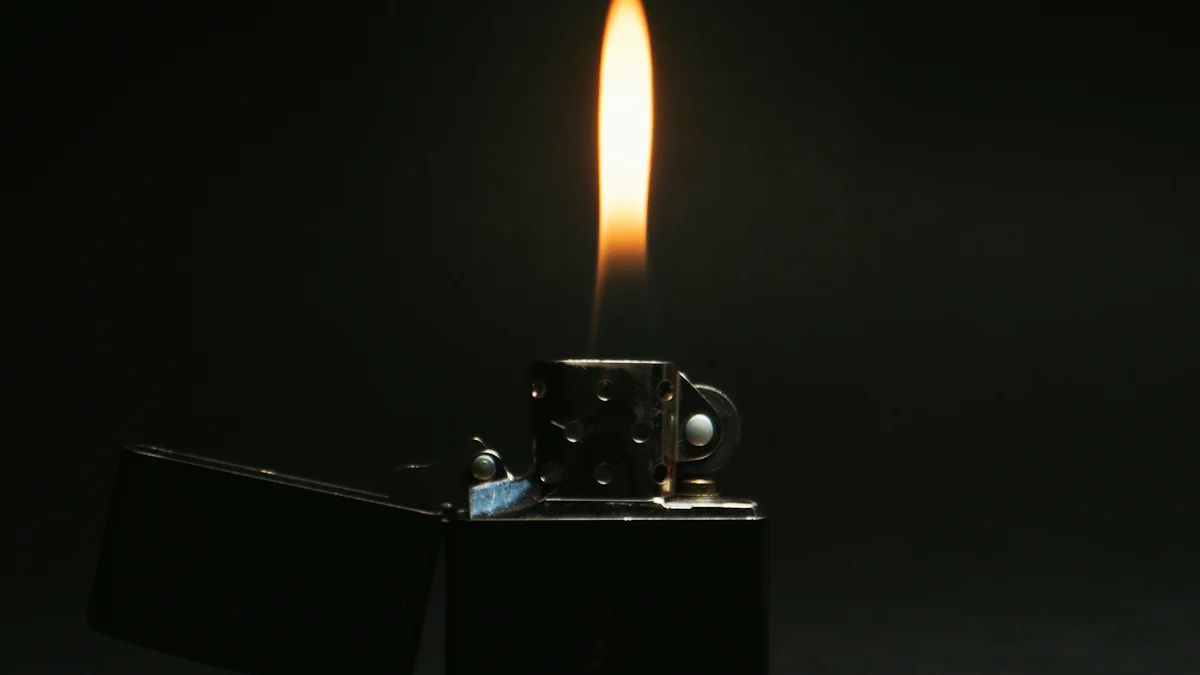
Streamlining workflow efficiency is crucial for optimizing lighter production equipment. By focusing on mapping out production processes and implementing lean manufacturing principles, you can significantly enhance productivity.
Map Out Production Processes
Mapping out production processes provides a clear understanding of each step involved in manufacturing. You should start by documenting every stage of the production line. This documentation helps identify bottlenecks and areas where improvements are needed. Use flowcharts or diagrams to visualize the entire process. These tools make it easier to spot inefficiencies and redundancies. Once you have a clear map, analyze each step to determine if it adds value. Eliminate any unnecessary actions that do not contribute to the final product. By refining the production process, you ensure that your lighter production equipment operates smoothly and efficiently.
Implement Lean Manufacturing Principles
Lean manufacturing principles focus on reducing waste and improving efficiency. You should adopt these principles to enhance the performance of lighter production equipment. Start by identifying waste in your production line. Waste can include excess inventory, overproduction, and unnecessary movement. Once identified, work on eliminating these inefficiencies. Encourage your team to participate in this process. Their insights can be valuable in finding innovative solutions. Implement continuous improvement practices, such as Kaizen, to foster a culture of ongoing enhancement. Regularly review and adjust your processes to maintain optimal efficiency. By embracing lean manufacturing, you create a streamlined production line that maximizes output and minimizes waste.
Upskill the Workforce for Lighter Production Equipment
Enhancing the skills of your workforce is crucial for optimizing the performance of lighter production equipment. A skilled team can operate machinery efficiently, troubleshoot issues quickly, and contribute to overall productivity. By investing in your employees’ development, you ensure that your production line runs smoothly and effectively.
Provide Ongoing Training Programs
Ongoing training programs are essential for keeping your workforce up-to-date with the latest technologies and best practices. Regular training sessions help employees understand new equipment features and improve their operational skills. You should organize workshops and seminars that focus on specific aspects of lighter production equipment. These sessions can cover topics such as machine maintenance, safety protocols, and quality control techniques. Encourage employees to participate actively and ask questions. This engagement fosters a deeper understanding and retention of knowledge. Additionally, consider offering online courses or certifications to provide flexible learning opportunities. By prioritizing continuous education, you empower your team to excel in their roles and contribute to the efficiency of the production line.
Foster a Culture of Continuous Improvement
Creating a culture of continuous improvement is vital for sustaining efficiency in lighter production equipment. Encourage your employees to identify areas for enhancement and suggest innovative solutions. Regularly hold team meetings to discuss performance metrics and set improvement goals. Recognize and reward employees who contribute valuable ideas or demonstrate exceptional performance. This recognition motivates others to engage in the improvement process. Implement feedback mechanisms that allow employees to share their insights and experiences. By valuing their input, you create an environment where everyone feels responsible for the success of the production line. Continuous improvement not only boosts efficiency but also enhances job satisfaction and morale. By fostering this culture, you ensure that your production line remains competitive and adaptable to changing demands.
To boost efficiency in your lighter production line, focus on key strategies. Implement quality control measures and train your workforce. Utilize advanced technology and conduct root cause analysis. Leverage data analysis to gain insights and streamline workflows. Upskill your team through ongoing training and foster a culture of continuous improvement. By adopting these data-driven solutions, you enhance productivity and reduce waste. The long-term benefits include cost savings and increased competitiveness. Embrace these practices to ensure your production line operates at peak efficiency, driving success for your business.
FAQ
What is the first time yield in lighter production?
First time yield refers to the percentage of products manufactured correctly without any defects on the first attempt. It measures the efficiency and quality of the production process. A high first time yield indicates fewer defects and less rework, leading to cost savings and increased productivity.
How can I improve defect detection in my production line?
You can enhance defect detection by investing in advanced technology like automated vision systems and sensors. These tools provide real-time monitoring and high precision in identifying defects. Conducting regular root cause analysis also helps in understanding and addressing the underlying issues causing defects.
Why is data analysis important in production efficiency?
Data analysis provides insights into your production processes. By analyzing data, you can identify patterns, inefficiencies, and areas for improvement. This information allows you to make informed decisions that optimize performance and enhance efficiency.
What are lean manufacturing principles?
Lean manufacturing principles focus on reducing waste and improving efficiency. They involve identifying and eliminating non-value-added activities in the production process. Implementing these principles helps streamline operations, maximize output, and minimize waste.
How can I upskill my workforce effectively?
Provide ongoing training programs that focus on the latest technologies and best practices. Organize workshops and seminars on specific aspects of lighter production equipment. Encourage active participation and offer online courses for flexible learning opportunities.
What role does quality control play in production efficiency?
Quality control ensures that products meet required standards before leaving the production line. Implementing robust quality control measures helps identify defects early, reducing waste and improving product quality. Regular inspections and testing are essential components of an effective quality control system.
How do I create a culture of continuous improvement?
Encourage employees to identify areas for enhancement and suggest solutions. Hold regular team meetings to discuss performance metrics and set improvement goals. Recognize and reward contributions to motivate engagement in the improvement process.
What are the benefits of streamlining workflow efficiency?
Streamlining workflow efficiency reduces bottlenecks and redundancies in the production process. It leads to smoother operations, increased productivity, and reduced production time. Mapping out production processes and implementing lean manufacturing principles are effective strategies for achieving this.
How does advanced technology contribute to production efficiency?
Advanced technology, such as automated inspection systems and IoT devices, enhances speed and accuracy in production. These tools provide real-time feedback and allow for immediate issue resolution, ensuring high-quality products and efficient operations.
Why is it important to train employees on best practices?
Training employees on best practices ensures they understand standard operating procedures and can quickly address potential issues. Well-trained employees contribute to minimizing downtime and optimizing the performance of production equipment. Regular training sessions keep the team updated on the latest techniques and technologies.