Proper care of your gas fill machine plays a vital role in ensuring its safety, efficiency, and durability. Regular maintenance keeps the equipment running smoothly and prevents unexpected breakdowns. A proactive approach allows you to identify minor issues early, reducing costly repairs and downtime. It also enhances operational efficiency by improving production quality and minimizing waste. By maintaining your machine, you not only extend its lifespan but also create a safer working environment. This approach ensures that your gas operations remain reliable and cost-effective over time.
Key Takeaways
- Regular maintenance is crucial for the safety, efficiency, and longevity of your gas fill machine. Schedule routine inspections to catch minor issues before they escalate.
- Familiarize yourself with your machine’s components and the manufacturer’s manual. This knowledge is essential for effective operation and maintenance.
- Perform daily visual inspections to identify leaks or worn parts. Create a checklist to ensure all critical areas are covered consistently.
- Clean and lubricate your machine regularly to prevent buildup and reduce friction, which enhances performance and minimizes downtime.
- Store your gas fill machine in a clean, dry, and well-ventilated area to protect it from rust and damage, ensuring optimal functionality.
- Implement safety protocols and prepare for emergencies to protect both operators and equipment, enhancing overall operational safety.
- Invest in monitoring systems and professional servicing to optimize performance and reduce unexpected breakdowns, ensuring long-term reliability.
Understand Your Gas Fill Machine
Understanding your gas fill machine is the first step toward ensuring its peak performance. Familiarizing yourself with its design, components, and functionality allows you to operate it efficiently and address potential issues before they escalate. This knowledge forms the foundation for effective maintenance and safe operation.
Read the Manufacturer’s Manual
The manufacturer’s manual is your most reliable guide. It provides detailed instructions on operating, maintaining, and troubleshooting your gas fill machine. Take time to read it thoroughly. Pay attention to the recommended maintenance schedule and safety precautions. The manual also outlines the specifications of the machine, helping you understand its capabilities and limitations. Keeping this document accessible ensures you can refer to it whenever needed.
“Knowledge about gas filling machines is essential, especially for those in industries that require these machines.” – Industry Experts
By following the manual, you reduce the risk of errors and ensure compliance with the manufacturer’s guidelines. This practice not only extends the lifespan of your equipment but also enhances its efficiency.
Identify Key Components
Knowing the key components of your gas fill machine is crucial. These parts include the compressor, valves, pressure gauges, and hoses. Each component plays a specific role in the gas filling process. For example, the compressor pressurizes the gas, while the valves control its flow. Regularly inspecting these parts helps you detect wear and tear early.
Create a checklist of the main components and their functions. This approach simplifies routine inspections and ensures no part is overlooked. Understanding how these components interact allows you to identify potential issues quickly. It also empowers you to communicate effectively with technicians during servicing.
Pro Tip: Choose machines designed for easy maintenance. This feature reduces downtime and simplifies the servicing process.
By mastering the basics of your gas fill machine, you set the stage for efficient operation and long-term reliability.
Regular Inspections and Maintenance Practices
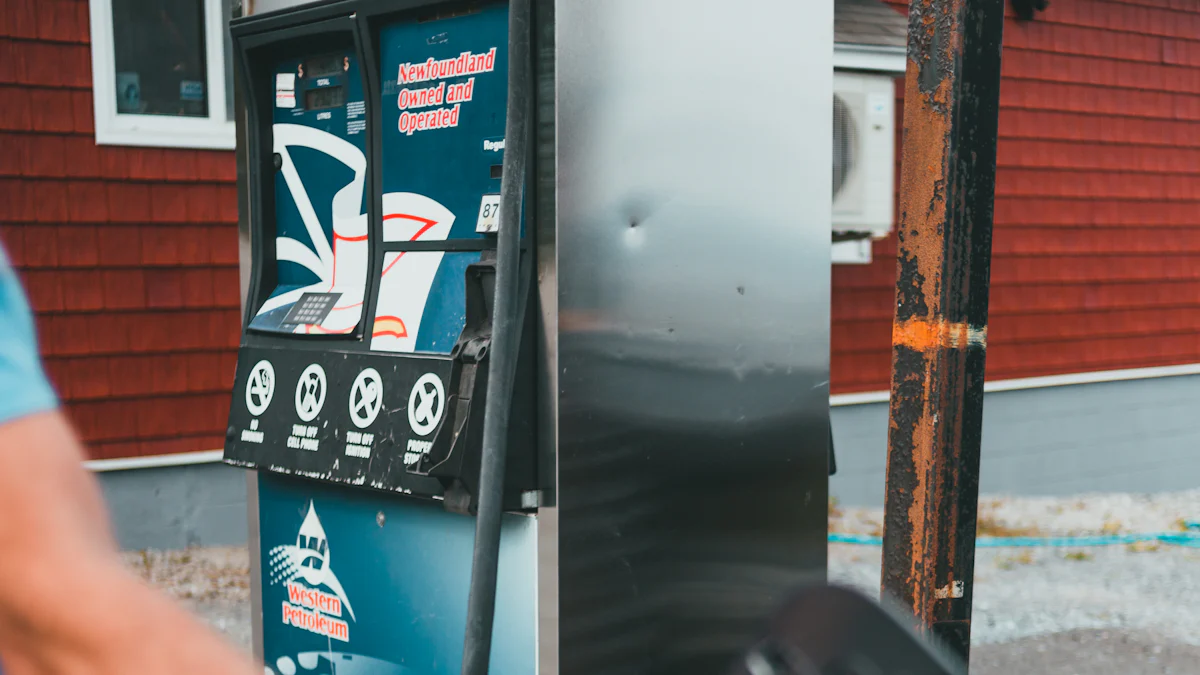
Regular inspections and maintenance are essential for keeping your gas fill machine in top condition. By adopting a proactive approach, you can prevent costly breakdowns and ensure the equipment operates efficiently. These practices not only extend the lifespan of your machine but also enhance safety and productivity.
Perform Routine Inspections
Routine inspections are the foundation of effective maintenance. You should visually inspect your gas fill machine daily to identify potential issues such as leaks, worn-out parts, or unusual noises. Pay close attention to critical components like valves, hoses, and pressure gauges. Early detection of problems allows you to address them before they escalate into major repairs.
Create a checklist for your inspections. This ensures you cover all essential areas and maintain consistency. For example, check for loose connections, monitor pressure levels, and examine the compressor for signs of wear. Regular inspections also help you comply with safety standards, reducing the risk of accidents during operation.
“Adopting a proactive approach to gas cylinder maintenance can significantly extend their lifespan and ensure their safety and performance.” – Industry Best Practices
By performing routine inspections, you safeguard the reliability and efficiency of your gas fill machine.
Clean and Lubricate Components
Cleaning and lubrication are vital aspects of routine maintenance. Dust, debris, and residue can accumulate on your machine over time, affecting its performance. After each production cycle, clean the machine thoroughly to prevent buildup that could damage mechanical components. Use compressed air to blow out the fan and cooling fins every 100 hours to maintain optimal cooling.
Lubrication reduces friction between moving parts, ensuring smooth operation. Apply the recommended lubricants to components like bearings and valves. Follow the manufacturer’s guidelines to avoid over-lubrication, which can attract dirt and cause additional wear. Regular cleaning and lubrication not only improve efficiency but also minimize the risk of unexpected downtime.
Replace Worn-Out Parts
Replacing worn-out parts is a crucial step in maintaining your gas fill machine. Over time, components like hoses, seals, and filters may degrade due to constant use. Ignoring these issues can lead to reduced performance or even complete failure of the machine. Conduct regular inspections to identify parts that need replacement.
Keep spare parts readily available to minimize downtime. When replacing components, always use genuine parts recommended by the manufacturer. This ensures compatibility and maintains the integrity of your machine. Scheduling regular professional maintenance can also help you identify and replace worn-out parts effectively.
Pro Tip: Machines designed for easy maintenance simplify the process of replacing parts, saving you time and effort.
By prioritizing the replacement of worn-out parts, you enhance the durability and reliability of your gas fill machine.
Storage and Handling Guidelines for Gas Fill Machines
Proper storage and careful handling of your gas fill machine are essential for maintaining its performance and ensuring safety. Neglecting these aspects can lead to equipment damage, reduced efficiency, or even hazardous situations. By following these guidelines, you can protect your machine and optimize its functionality.
Store in a Safe Environment
Storing your gas fill machine in a safe and suitable environment is crucial. Choose a location that is clean, dry, and well-ventilated. Avoid areas with excessive moisture, as it can cause rust and corrosion, which may compromise the machine’s performance. Ensure the storage space is free from dust and debris, as these can infiltrate the machine and affect its components.
Place the machine on a stable, non-combustible platform to prevent accidents. Keep it away from flammable materials and direct sunlight, as extreme heat can damage sensitive parts. If your machine operates with gas cylinders, store the cylinders in a well-drained area to avoid leaks and ensure safety.
“The first thing to consider when purchasing a gas filling machine is the size and capacity of the machine. You need to make sure that the machine is large enough to accommodate the size and number of gas cylinders that you need to fill.” – Gas Filling Machine Expert
By providing a secure and appropriate storage environment, you extend the lifespan of your gas fill machine and maintain its peak performance.
Handle with Care
Handling your gas fill machine with care is just as important as proper storage. Always follow the manufacturer’s instructions when moving or operating the machine. Use appropriate tools and equipment to lift or transport it, avoiding unnecessary strain on its components. Mishandling can lead to leaks, damage, or reduced performance.
Inspect the machine before and after each use to identify any signs of wear or potential issues. Pay close attention to hoses, valves, and connections, as these areas are prone to leaks. Address any problems immediately to prevent further damage. Train your staff on proper handling techniques to ensure consistent care and minimize risks.
Avoid exposing the machine to sudden impacts or vibrations, as these can loosen parts and affect its functionality. Handle gas cylinders with equal caution, ensuring they are securely attached and free from leaks. Proper handling practices not only enhance the machine’s performance but also create a safer working environment.
By prioritizing careful handling, you reduce the likelihood of accidents and maintain the reliability of your gas fill machine.
Safety Measures for Operating Gas Fill Machines
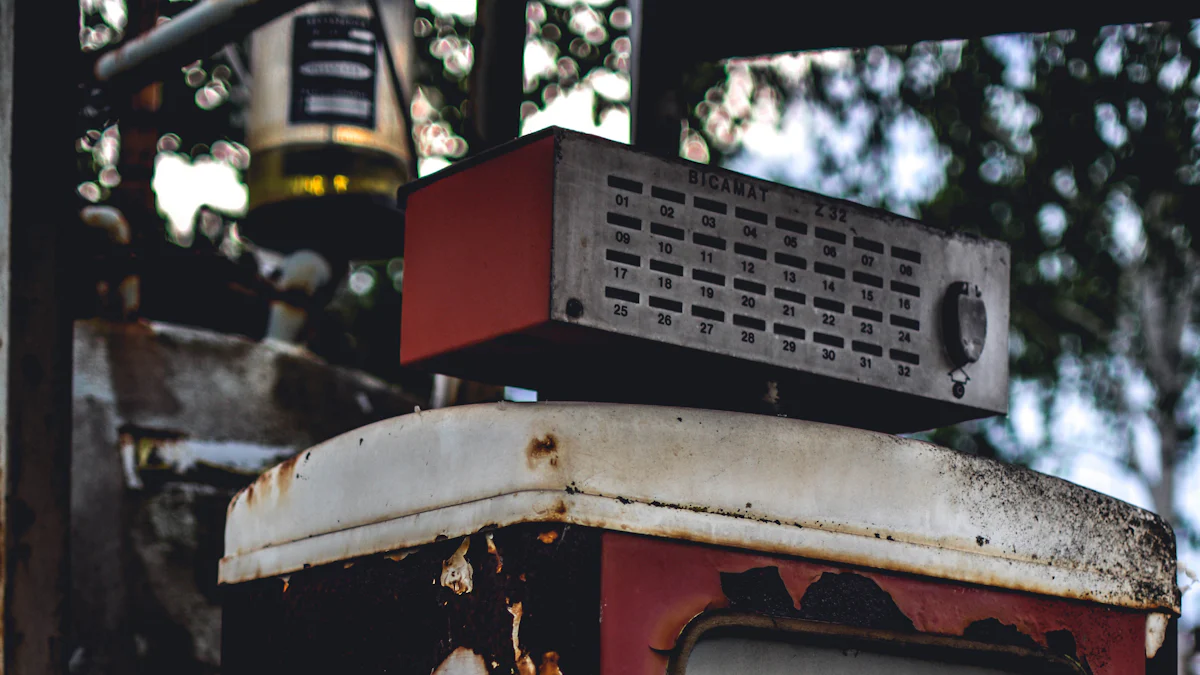
Operating a gas fill machine requires strict adherence to safety measures to protect both the equipment and the operators. By following established protocols and preparing for emergencies, you can ensure a safe and efficient working environment.
Follow Safety Protocols
Safety protocols are essential when working with gas fill machines. These guidelines help you minimize risks and maintain control during operations. Always inspect the machine before use to ensure all components, such as valves and pressure gauges, are functioning correctly. Verify that there are no leaks or loose connections.
Equip your gas fill machine with safety features like pressure relief valves, flame arrestors, and emergency shut-off switches. These features act as safeguards, preventing accidents in case of malfunctions. Ensure that all operators are trained to use these features effectively.
Tip: Keep a checklist of safety protocols near the machine. This serves as a quick reference for operators and reinforces safe practices.
Wear appropriate personal protective equipment (PPE), including gloves, goggles, and flame-resistant clothing. Avoid distractions while operating the machine, and never leave it unattended during use. Following these protocols reduces the likelihood of accidents and ensures smooth operations.
Prepare for Emergencies
Emergency preparedness is a critical aspect of maintaining safety in gas operations. Develop a comprehensive emergency response plan tailored to your facility. This plan should address potential incidents, such as gas leaks, equipment failures, or cylinder ruptures. Regularly review and update the plan to account for new risks or changes in equipment.
Train your team to respond effectively during emergencies. Conduct drills to familiarize them with evacuation routes, shut-off procedures, and first-aid measures. Ensure that emergency shut-off switches on the gas fill machine are easily accessible and functional.
“Emergency preparedness is not just about having a plan; it’s about ensuring everyone knows their role during a crisis.” – Safety Experts
Keep fire extinguishers, spill kits, and first-aid supplies readily available. Label these items clearly and place them in easily accessible locations. In addition, maintain open communication channels to report emergencies promptly and coordinate responses efficiently.
By preparing for emergencies, you create a safer environment and minimize the impact of unexpected incidents. This proactive approach protects both your team and your equipment.
Advanced Tips for Improving Efficiency
Enhancing the efficiency of your gas fill machine requires adopting advanced strategies that go beyond basic maintenance. By leveraging modern tools and professional services, you can optimize the performance of your equipment and streamline operations. These advanced practices ensure that your machine operates at its best while reducing downtime and costs.
Use Monitoring Systems
Monitoring systems play a vital role in improving the performance of your gas fill machine. These systems provide real-time data on critical parameters such as pressure, temperature, and flow rates. By tracking this information, you can identify irregularities early and take corrective actions before they escalate into major issues.
Modern monitoring technology also enables predictive maintenance. With data analysis, you can anticipate when components might fail and schedule repairs proactively. This approach minimizes unexpected breakdowns and ensures uninterrupted operation. Additionally, monitoring systems help you maintain compliance with safety standards by alerting you to potential risks like leaks or overpressure.
“Real-time monitoring and predictive analytics allow operators to prevent unexpected breakdowns and optimize machine performance.” – Industry Insights
Investing in monitoring systems not only boosts efficiency but also extends the lifespan of your equipment. This practice is essential for businesses aiming to achieve long-term reliability and cost savings.
Schedule Professional Servicing
Professional servicing is a cornerstone of maintaining the efficiency and performance of your gas fill machine. While routine maintenance covers daily and weekly tasks, professional servicing provides a deeper level of care. Trained technicians can perform detailed inspections, tune-ups, and adjustments that go beyond what regular checks can achieve.
Scheduling professional servicing ensures that your machine operates at peak performance. Technicians use specialized tools to detect hidden issues and replace worn-out parts with precision. They also update software and calibrate components to maintain accuracy and efficiency. This level of expertise reduces the risk of operational errors and enhances the overall reliability of your equipment.
Pro Tip: Choose machines with strong after-sales support. Reliable support simplifies servicing and ensures your equipment remains in top condition.
Regular professional servicing complements your maintenance practices and helps you avoid costly repairs. It also provides peace of mind, knowing that your machine is in expert hands.
Implement Digital Inventory Systems
Digital inventory systems are essential for optimizing gas management efficiency. These systems allow you to track gas cylinders, monitor usage patterns, and manage stock levels effectively. By integrating inventory data with your gas fill machine, you can automate processes like cylinder changeovers and refills, saving time and reducing manual errors.
A digital inventory system also supports better decision-making. With accurate data, you can forecast demand, plan purchases, and avoid overstocking or shortages. This optimization improves operational efficiency and reduces waste. Additionally, these systems enhance safety by ensuring that cylinders are stored and handled according to best practices.
“Advanced features like data integration and automatic changeovers improve efficiency in businesses dealing with diverse liquid products.” – Efficiency Experts
Implementing a digital inventory system streamlines your operations and maximizes the performance of your gas fill machine. This technology is a valuable investment for businesses seeking to stay competitive and efficient.
By adopting these advanced tips, you elevate the efficiency and reliability of your gas fill machine. Monitoring systems, professional servicing, and digital inventory systems work together to optimize operations, reduce downtime, and enhance safety. These practices represent the best approach to achieving long-term success in gas management.
Understanding your gas fill machine and maintaining it properly ensures safety, efficiency, and long-term reliability. Regular inspections, cleaning, and part replacements keep the equipment in optimal condition. Proper storage and careful handling prevent damage and enhance performance. Adhering to safety measures protects both operators and the machine. Advanced techniques like monitoring systems and professional servicing improve efficiency and reduce downtime. Implement these practices to maximize the benefits of your equipment. Start today by consulting the manual, training your team, or scheduling professional servicing to secure the future of your operations.
FAQ
What are gas filling machines used for?
Gas filling machines are designed to fill various gases, such as oxygen, nitrogen, and carbon dioxide, into containers like cylinders and bottles. These machines ensure precise gas injection, making them essential for industries that require accurate gas concentrations.
What industries use gas filling machines?
Gas filling machines serve a wide range of industries, including automotive, pharmaceutical, food and beverage, and chemical sectors. They play a vital role in ensuring efficient gas cylinder management by accurately filling containers used in these fields.
What are the advantages of using gas filling machines?
Gas filling machines offer several benefits. They provide efficient and accurate gas filling, reducing manual labor and saving time. Their precision ensures consistent results, which is critical for industries that rely on high-quality gas cylinder management.
What are the disadvantages of gas filling machines?
While gas filling machines are highly effective, they come with certain challenges. They can be expensive to purchase and maintain. Operating them often requires specialized training, which adds to the overall cost and complexity.
What properties should you consider before purchasing a gas filling machine?
When selecting a gas filling machine, focus on properties like accuracy, speed, safety, and flexibility. These features ensure the machine meets your operational needs and supports efficient gas cylinder management.
What role do gas filling machines play in various industries?
Gas filling machines are indispensable in many industries. They ensure accurate and efficient filling of gas cylinders and bottles, which is crucial for maintaining safety and productivity. Their role extends to improving gas cylinder maintenance practices by minimizing errors and wear.
What is gas filling equipment designed to do?
Gas filling equipment is engineered to inject specific gases at precise concentrations. This capability ensures the equipment meets the exact requirements of industries that depend on accurate gas cylinder maintenance.
How can you maintain gas filling machines effectively?
To maintain gas filling machines, perform regular inspections, clean and lubricate components, and replace worn-out parts. Proper gas cylinder maintenance practices, such as storing cylinders in safe environments, also contribute to the longevity and efficiency of the machines.
Are gas filling machines suitable for small-scale operations?
Yes, gas filling machines can be tailored to suit small-scale operations. Compact models with user-friendly features are available, making them accessible for businesses with limited space or lower production demands.
How do gas filling machines improve safety?
Gas filling machines enhance safety by ensuring precise gas filling and reducing the risk of leaks or overpressure. Features like pressure relief valves and emergency shut-off switches further protect operators and equipment during use.