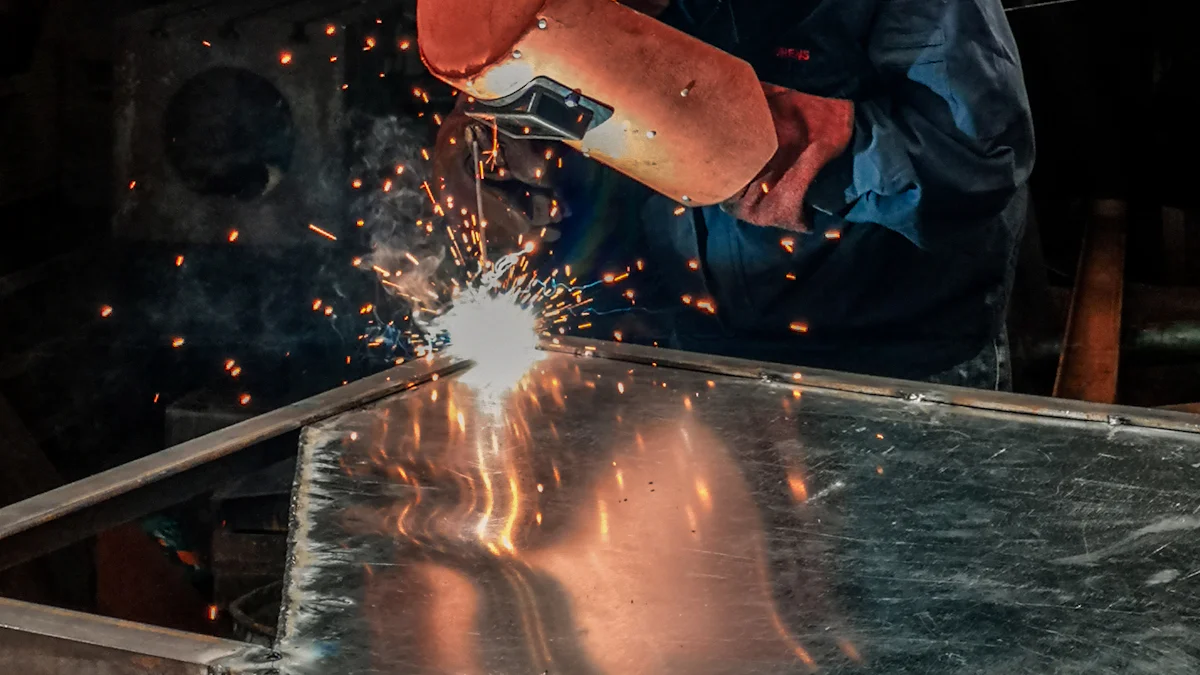
Regular maintenance plays a vital role in keeping your fully automatic welding machine efficient and safe. It ensures the machine operates smoothly, reducing the risk of unexpected breakdowns. Proper care extends the machine’s lifespan and helps you avoid expensive repairs. Consistent upkeep also guarantees high-quality welds, which are essential for professional results. By dedicating time to maintenance, you minimize downtime and maintain productivity. A well-maintained machine not only performs better but also provides a safer working environment for you and your team.
Key Takeaways
- Regular maintenance is crucial for the efficiency and safety of your welding machine, helping to prevent unexpected breakdowns and costly repairs.
- Daily cleaning with non-abrasive tools and mild solutions keeps your machine free from contaminants, enhancing its performance and lifespan.
- Conduct daily inspections to identify wear and damage early, ensuring that critical components like contact tips and nozzles are in good condition.
- Properly lubricate moving parts using manufacturer-recommended products to reduce friction and extend the life of your machine.
- Stay proactive by scheduling professional maintenance at least once a year to address complex issues that may not be visible during routine checks.
- Always follow the manufacturer’s guidelines for maintenance tasks to avoid damaging your machine and ensure optimal performance.
- Prioritize safety by disconnecting the power supply before maintenance and wearing appropriate personal protective equipment (PPE).
Daily Maintenance Tips for Fully Automatic Welding Machines
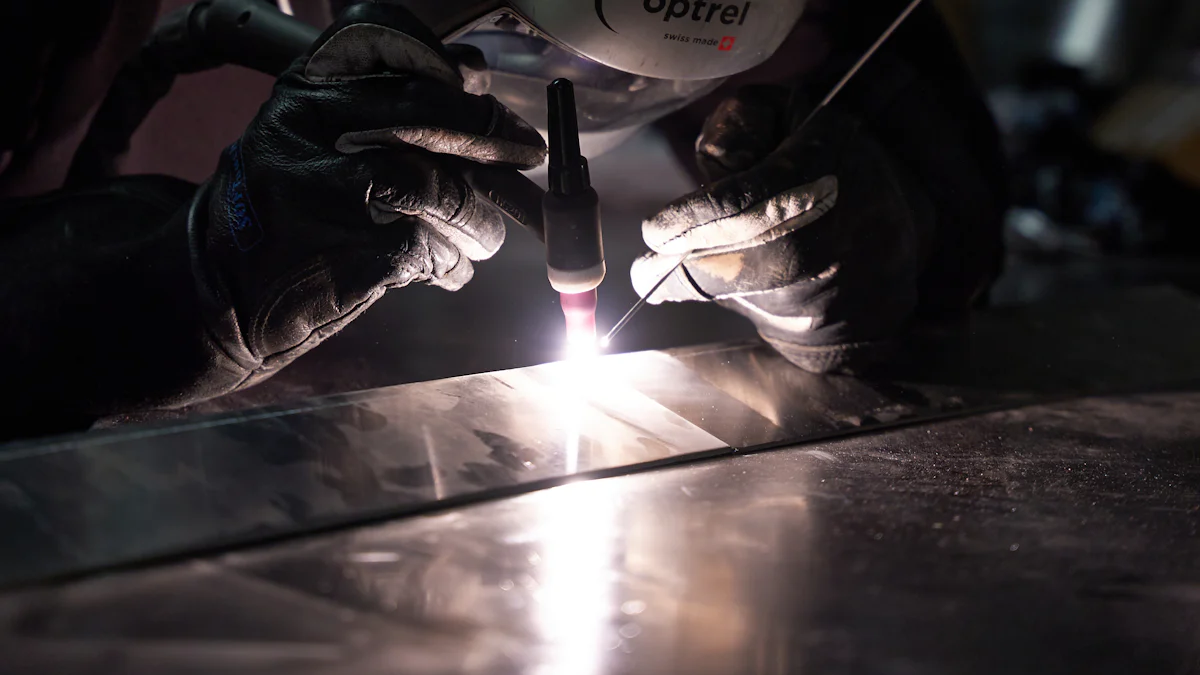
Clean the Machine Thoroughly
Keeping your fully automatic welding machine clean ensures optimal performance. Dust, debris, and welding residue can accumulate quickly, affecting the machine’s efficiency. Use non-abrasive tools to remove these contaminants without damaging the surface. A soft brush or cloth works well for this task. For deeper cleaning, apply mild soapy water or specialized cleaning solutions recommended by the manufacturer. Avoid harsh chemicals that might corrode the machine’s components. Regular cleaning not only improves functionality but also extends the machine’s lifespan.
Inspect and Protect the Machine
Daily inspections help you identify potential issues before they escalate. Check for visible wear, loose parts, or any signs of damage. Pay close attention to critical components like the contact tips and nozzles, as these directly impact weld quality. If you notice any irregularities, address them immediately to prevent further complications. When the machine is not in use, cover it with a protective sheet. This simple step shields it from dust and moisture, preserving its condition and ensuring consistent performance.
Power Down Safely
Proper shutdown procedures are essential for maintaining the safety and longevity of your fully automatic welding machine. Always follow the manufacturer’s guidelines when powering down the equipment. Abruptly turning off the machine can lead to electrical issues or data loss in advanced models. During extended periods of inactivity, disconnect the power supply entirely. This precaution reduces the risk of electrical surges and protects the machine from potential damage. A safe shutdown routine safeguards both the equipment and your workspace.
Periodic Maintenance for Fully Automatic Welding Machines
Periodic maintenance ensures your fully automatic welding machine operates efficiently over time. By addressing key components regularly, you can prevent wear and maintain consistent performance. Follow these steps to keep your equipment in top condition.
Lubricate Moving Components
Proper lubrication reduces friction and extends the life of moving parts. Use lubricants recommended by the manufacturer to avoid compatibility issues. Apply them sparingly to prevent dust and debris from sticking to the surfaces. Excess lubrication can attract contaminants, which may hinder the machine’s performance. Focus on areas with frequent motion, such as joints and bearings, to ensure smooth operation.
Perform Electrical System Inspections
Electrical systems are critical for the functionality of your welding machine. Inspect wiring, connections, and fuses for visible signs of wear or damage. Loose or frayed wires can lead to power inconsistencies or safety hazards. Test voltage levels using a multimeter to confirm a stable power supply. Address any irregularities immediately to avoid further complications. Regular checks help you identify potential issues before they escalate into costly repairs.
Align and Adjust Machine Components
Alignment plays a vital role in achieving precise welds. Verify that all welding parts are properly aligned to maintain accuracy. Misaligned components can result in poor weld quality and increased material waste. Adjust the machine settings as needed to match the requirements of your project. Refer to the manufacturer’s guidelines to ensure optimal performance. Regular adjustments keep your machine reliable and ready for any task.
Specialized Maintenance for Fully Automatic Welding Machines
Update Software and Firmware
Keeping your fully automatic welding machine up to date ensures optimal performance and security. Manufacturers often release software and firmware updates to enhance functionality and address vulnerabilities. Regularly check for these updates on the manufacturer’s website or through their support channels. Install them promptly to take advantage of improved features and bug fixes. Updated software can also optimize the machine’s efficiency, helping you achieve consistent results. Always verify that the updates are compatible with your specific model before installation.
Conduct Comprehensive Safety Inspections
Safety inspections are essential for maintaining a secure work environment. Test emergency stops, sensors, and other safety features to confirm they function correctly. Faulty safety mechanisms can lead to accidents or equipment damage. Use the manufacturer’s guidelines to perform these tests accurately. Ensure your machine complies with workplace safety regulations by reviewing local and industry-specific standards. Address any deficiencies immediately to avoid potential hazards. Regular safety checks protect both the operator and the equipment.
Schedule Professional Maintenance
Professional maintenance provides a deeper level of care for your welding machine. Hire certified technicians to conduct thorough inspections and handle complex repairs. These experts have the tools and knowledge to identify issues that may not be visible during routine checks. Schedule professional servicing at least once a year or as recommended by the manufacturer. Keep detailed records of all maintenance activities, including dates, services performed, and parts replaced. These records help you track the machine’s condition and plan future maintenance effectively.
Common Mistakes to Avoid During Maintenance
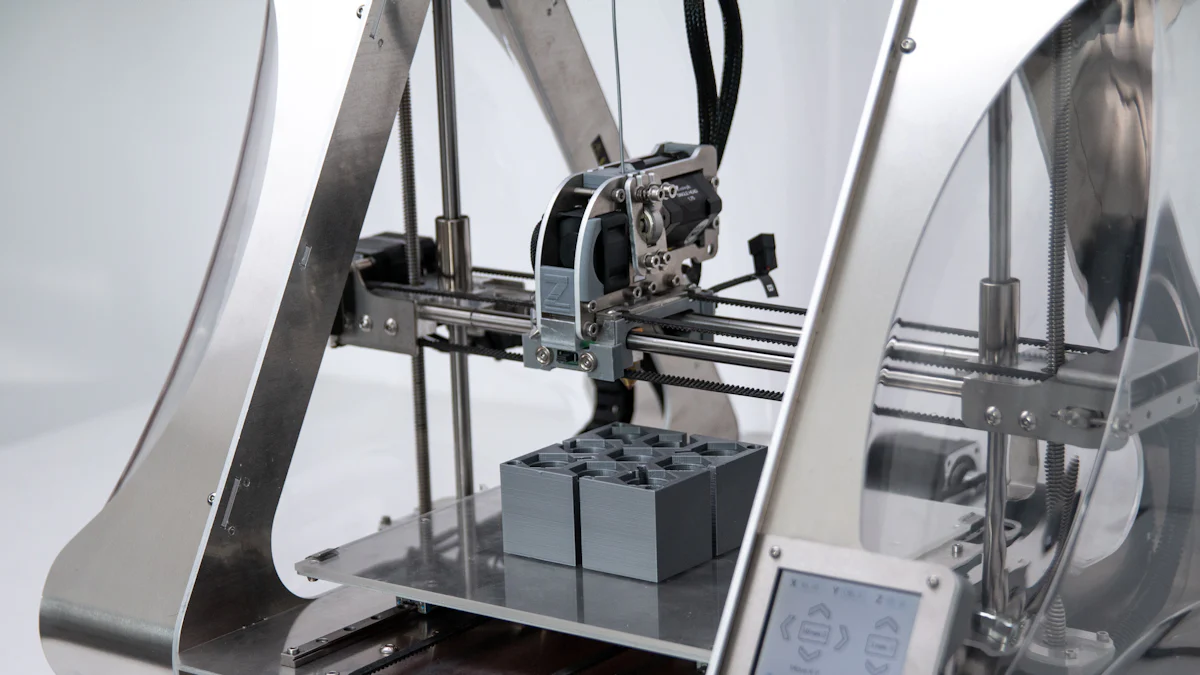
Ignoring Manufacturer’s Guidelines
Always follow the user manual for specific maintenance instructions.
The manufacturer’s guidelines provide essential details tailored to your welding machine. Skipping these instructions can lead to improper maintenance, which may damage the equipment. Read the user manual thoroughly and refer to it whenever you perform maintenance tasks. It contains step-by-step procedures and recommendations that ensure you handle the machine correctly.
Avoid using generic tools or products that may harm the machine.
Using tools or products not designed for your welding machine can cause significant damage. Generic tools might not fit properly, leading to wear or misalignment. Stick to manufacturer-approved tools and cleaning products. These are specifically designed to maintain the machine’s integrity and performance. Avoid experimenting with substitutes, as they may compromise the machine’s functionality.
Skipping Scheduled Maintenance
Understand the risks of neglecting regular maintenance.
Neglecting scheduled maintenance increases the likelihood of unexpected breakdowns. Over time, components wear out and require attention. Ignoring these needs can result in costly repairs or even permanent damage. Regular maintenance ensures the machine operates efficiently and prevents small issues from escalating into major problems.
Set and adhere to a preventive maintenance schedule.
A preventive maintenance schedule helps you stay organized and proactive. Create a checklist of tasks based on the manufacturer’s recommendations. Mark specific dates for inspections, cleaning, and part replacements. Consistently following this schedule keeps your machine in optimal condition. It also reduces downtime and enhances productivity.
Overlooking Safety Measures
Disconnect the power supply before performing any maintenance.
Working on a powered machine poses serious safety risks. Always disconnect the power supply before starting any maintenance activity. This precaution prevents accidental electrical shocks or equipment activation. Double-check that the machine is completely powered down to ensure your safety.
Wear appropriate personal protective equipment (PPE) at all times.
Maintenance tasks expose you to potential hazards like sharp edges, electrical components, or chemical cleaners. Wearing PPE minimizes these risks. Equip yourself with gloves, safety goggles, and protective clothing. Ensure your PPE fits properly and meets safety standards. Prioritizing your safety protects you from injuries and ensures a secure working environment.
Daily, periodic, and specialized maintenance ensures your fully automatic welding machine operates at its best. Regular care improves efficiency, enhances safety, and extends the machine’s lifespan. By dedicating time to maintenance, you prevent costly repairs and avoid unexpected downtime. Establishing a consistent routine keeps your equipment reliable and ready for any task. Take proactive steps to maintain your machine, and you will enjoy long-term benefits in performance and productivity.
FAQ
What is the importance of maintaining a fully automatic welding machine?
Regular maintenance ensures your welding machine operates efficiently and safely. It minimizes downtime, prevents costly repairs, and extends the machine’s lifespan. Proper care also guarantees consistent weld quality, which is essential for professional results.
How often should I clean my welding machine?
You should clean your welding machine daily after use. Dust, debris, and welding residue can accumulate quickly, affecting performance. Regular cleaning helps maintain the machine’s efficiency and prevents long-term damage.
What tools and products should I use for cleaning?
Use non-abrasive tools like soft brushes or cloths to clean the machine. For deeper cleaning, apply mild soapy water or manufacturer-recommended cleaning solutions. Avoid harsh chemicals that could corrode or damage the components.
How can I identify potential issues during inspections?
Look for visible signs of wear, loose parts, or damage. Pay attention to critical components like contact tips, nozzles, and wiring. If you notice irregularities, address them immediately to prevent further complications.
Why is lubrication important for moving components?
Lubrication reduces friction and prevents wear on moving parts. It ensures smooth operation and extends the life of the machine. Always use lubricants recommended by the manufacturer to avoid compatibility issues.
When should I update the software or firmware of my welding machine?
Check for updates regularly on the manufacturer’s website or support channels. Install updates promptly to enhance performance, fix bugs, and address security vulnerabilities. Ensure the updates are compatible with your machine model.
What safety measures should I follow during maintenance?
Always disconnect the power supply before performing any maintenance tasks. Wear appropriate personal protective equipment (PPE), such as gloves, safety goggles, and protective clothing, to minimize risks and ensure your safety.
How often should I schedule professional maintenance?
Schedule professional maintenance at least once a year or as recommended by the manufacturer. Certified technicians can perform in-depth inspections and handle complex repairs that may not be visible during routine checks.
What are the risks of skipping scheduled maintenance?
Neglecting regular maintenance increases the likelihood of unexpected breakdowns. Over time, components wear out and require attention. Skipping maintenance can lead to costly repairs, reduced efficiency, and even permanent damage.
Can I use generic tools or products for maintenance?
Avoid using generic tools or products. They may not fit properly or could harm the machine. Stick to manufacturer-approved tools and cleaning products to maintain the machine’s integrity and performance.